Our Quality Testing Services
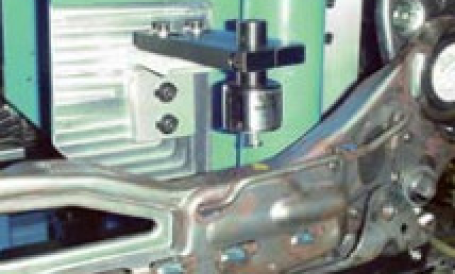
COMPLETE NVH SOLUTIONS
Signalysis offers a full range of test solutions. From expert consulting and customized software development to a complete turnkey test system, we will work with you to identify, develop and support a solution to meet your unique and specific requirements.
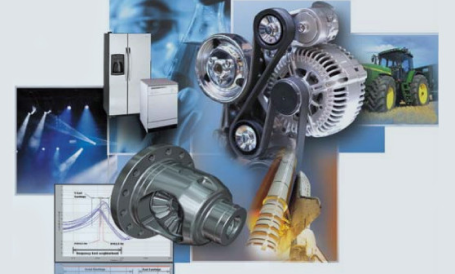
PROVEN TECHNOLOGY
Signalysis test systems are powered by our proprietary SigQC™ software. Backed by more than twenty years of development, SigQC is robust and configurable to any test application.

EXCEEDING EXPECTATIONS
Our automated solutions are designed to identify signatures in NVH and then correlate them back to a known root cause. We pride ourselves in providing each of our customers the ultimate solution experience with unsurpassed integrity.